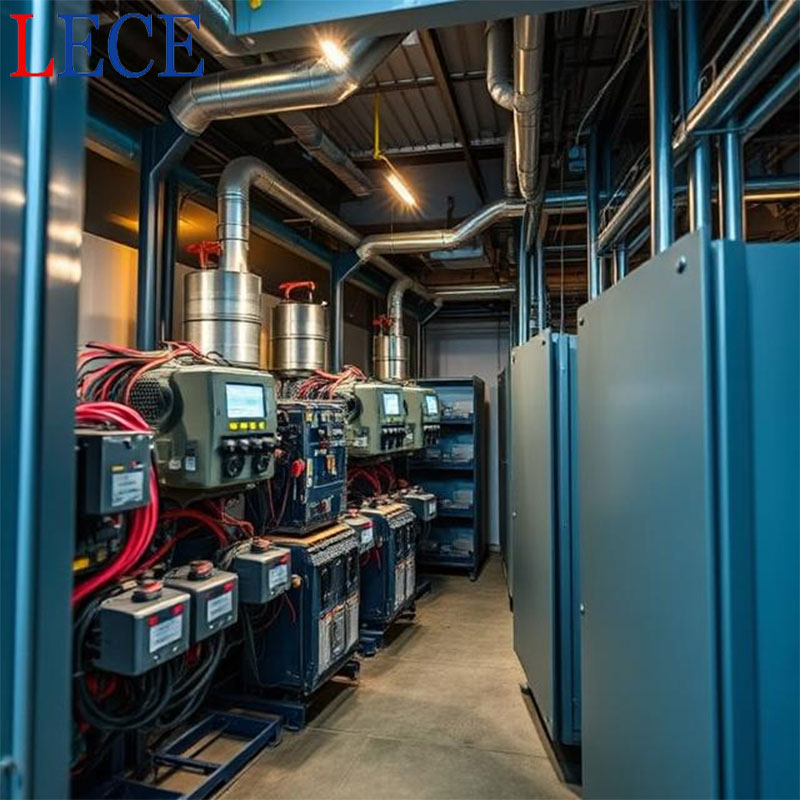
Downtime resulting from failed electrical and control components can be a costly and disruptive nightmare for any business or facility especially those involved in processing or production. Failing equipment is inevitable however the magnitude of its impact to the business does not have to be catastrophic. In most cases by implementing sound preventative maintenance practices operational impact can be mitigated and, in many cases, eliminated.
We find definite co-relation between high spends on reactive, emerging, emergency and callout work from businesses that do not have a planned and preventative maintenance strategy.
One powerful tool to mitigate these issues and reduce operational costs is the implementation of a critical spare’s strategy. This is a fairly straightforward process and this article provides a brief guide as to how you can implement a critical spares strategy.
What Are Critical Spares?
Critical spares are components, parts, or equipment that are essential for the uninterrupted operation of an industrial facility or production plant. These spares are vital to the functionality and reliability of critical systems and machinery. They serve as a safeguard against unforeseen equipment failures, reducing downtime, and minimizing the associated costs.
A well-defined critical spare strategy involves identifying, procuring, and maintaining these essential spare parts to ensure they are readily available when needed. The goal is to strike a balance between minimizing operational costs and mitigating the risks of unexpected breakdowns.
Why Should you have a Critical Spare Strategy
A critical spare strategy is a no-brainer for most businesses. Electrical parts ARE going to fail. Planning to have the part on hand when and where you need it and confirming supply chain makes sense for the following reasons.
Reactive specialized labor always comes at a Premium weather it comes in the form of a contractors minimum callout, an emergency callout fee or after hours. It costs more to react. On average the cost saving on Reactive vs Planned labour can be up to 100%.
Reduces the amount of time spent sourcing the part at short notice.
Reduces the cost of plant down time and the cost associated with that down time.
Increases plant safety
Actionable Checklist for Deciding if a Critical Spare Is Required
Before diving into the specifics of implementing an electrical critical spare strategy, it’s crucial to assess whether a particular component or part should be designated as a critical spare. To help make this determination, consider the following checklist:
Is the equipment vital to your operations? Will its failure result in significant downtime, production losses, or safety risks? YES/NO
How long does it take to procure the part or equipment if it fails? Can the equipment be source off the shelf. YES/NO
Will the down time cost exceed the cost of the equipment? YES/NO
How often does the equipment or component fail? Frequently/Infrequently/Rarely
What is the cost impact of that failure? High/Medium/Low
What is the Safety impact of that failure? High/Medium/Low
Does the equipment have an end of life and is there a viable alternative with a Like-for-like swap. YES/NO
If the answers to these questions suggest that a particular component or equipment is essential to the operation, has extended lead times for procurement, and presents significant risks and costs in case of failure, it should be considered a critical spare.
Examples of Electrical Critical Spares for a Production Plant
- The types of electrical critical spares required may vary depending on the nature of the production plant and the machinery used. Here are some common examples:
- Motor Starters and Contactors: Due to the repetitive operation Motor starters and contactors require replacement over time.
- Sensors and Switches: Sensors and switches used for monitoring and controlling various processes will fail especially if they are mechanical in operation.
- Emergency Backup Power Systems: Backup power systems, such as uninterruptible power supplies (UPS) generally have end of life specification from the manufacturer.
- Instrumentation and Measurement Devices Precision instrumentation, like flow meters, pressure transmitters and temperature sensors can be susceptible to surges and external factors such as heat and environmental factors.
- Motors and actuators Electro-mechanical equipment are prone to failure due to normal operational wear. Most manufacturers will provide end of life guides and historic data is helpful in determining when equipment is likely to fail.
Strategies to Reduce Stock Held On-Site
- While having an adequate supply of critical spares is essential, it's also important to optimize your inventory to reduce costs. Here are some strategies that electrical contractors and plant owners can implement to manage their spare parts more efficiently:
- Standardization: We strongly recommend working with your electrical engineers or electrical contractor to create a Standardize equipment and components list where feasible. This reduces the variety of spare parts needed, making inventory management more streamlined. It also makes contractor management much easier and provides guidelines to contractors working on the site. This also reduces the risk early failure due to substandard equipment installation onsite.
- Vendor Partnerships: Establish strong relationships with reliable vendors and negotiate favourable agreements for quick access to critical spares. Preferred pricing, consignment agreements, and vendor-managed inventory (VMI) programs can be advantageous depending on the size of the operation. You may even be able to have your incumbent electrical service provider agree to keep critical spares on your behalf.
- Maintenance and Condition Monitoring: Implement a proactive maintenance strategy and condition monitoring to extend the lifespan of critical components. Regular maintenance can help prevent unexpected failures, reducing the need for immediate replacement.
- Training and Skills Development: Invest in training for maintenance personnel to improve their skills in diagnosing and repairing equipment. A skilled workforce can reduce the reliance on spare parts and minimize downtime. An example of this is for ELV control equipment. You may be able to train your staff to diagnose and install the equipment providing they are not exposed to any electrical hazards.
- Categorize Critical Spares: Classify critical spares based on their importance, lead time for procurement, and frequency of failure. Not all critical spares are equal, and a tiered approach can help allocate resources more effectively.
- Regular Inventory Assessments: Conduct periodic reviews of your spare parts inventory to identify obsolete or rarely used items. Dispose of or repurpose these items to free up storage space and reduce holding costs.
- Spare Parts Optimization Software: Utilize inventory management software to track spare parts usage, predict future requirements, and optimize stock levels. These tools can help in making informed decisions about which items to keep in inventory.
- Centralized Spare Parts Hub: Consider consolidating critical spares in a central location for easy access. This reduces the risk of misplaced or forgotten inventory items.
- Just-in-Time Procurement: Implement a just-in-time procurement strategy for certain critical spares. This approach ensures that spare parts are ordered only when needed, reducing carrying costs.
Conclusion
Implementing an electrical critical spare strategy is a proactive approach to reducing operational costs and enhancing the reliability of industrial plants and facilities. By carefully selecting critical spares, optimizing inventory management, and following best practices, electrical contractors and plant owners can ensure smoother operations, minimize downtime, and save significant resources in the long run.
To sum it up, critical spares are not just spare parts; they are an insurance policy against the costly disruptions of unplanned downtime. A well-executed critical spare strategy is an investment that pays dividends in the form of increased productivity, safety, and cost savings.
So, don’t wait until your critical systems fail; start developing your electrical critical spare strategy today.
If you would like more information, you can contact LECE @ service@lecegroup.com.au. We can assist with information, assistance to develop critical spare plans, complete an assessment or assist with the assessment.
References & Additional Reading
Create a resilient spare parts management strategy | Schneider Electric (se.com)